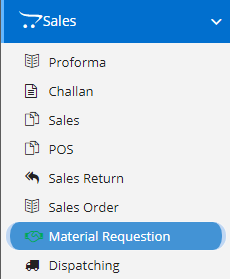
A material requisition, also known as a materials requisition form, or a material request, is a document used by the production department to request materials they need to complete a manufacturing process. It is used to authorize and keep a record of the components used so that an appropriate inventory can be stocked to keep production moving.
The production manager generally fills out the materials requisition form and delivers it to either the materials or storage department where all the raw materials are located. Then, the materials manager approves the request and has the raw materials moved from the storage area to the production floor.
The person who is requesting the materials will keep a copy of the form, as will the warehouse staff. An additional copy goes along with the picked goods to their eventual destination. If any items listed on the form are not in stock, another copy may go to the purchasing department so they can create a purchase requisition and purchase order to obtain the necessary materials.
Modules included in this module. We haven’t shown Product as it is a default sub-section without which Material Requisition is incomplete.
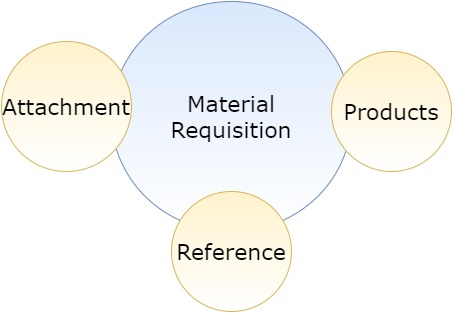
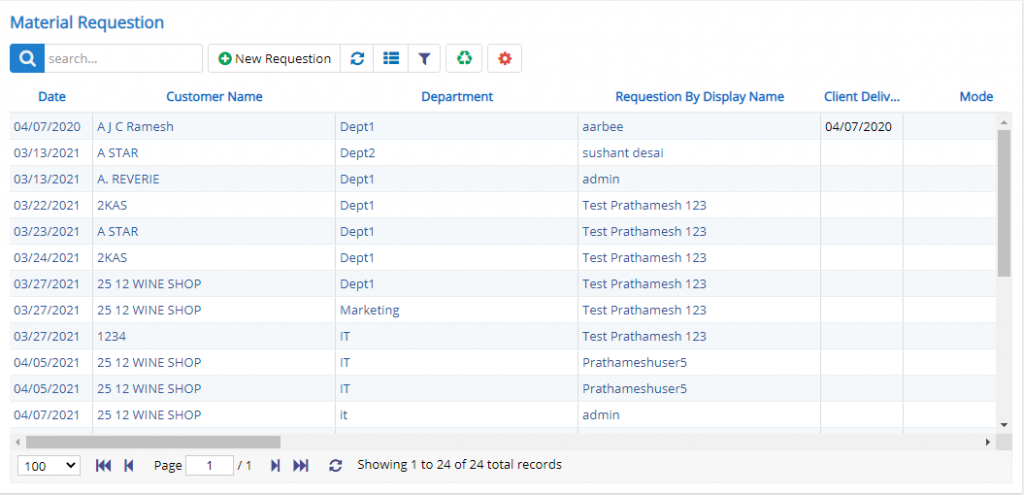
Here user can see the list of records already present in that form. Some common options like Excel export, PDF export, Filters, Reset Preferences and Settings are provided here. These buttons/options are visible only when the permissions or settings are enabled.
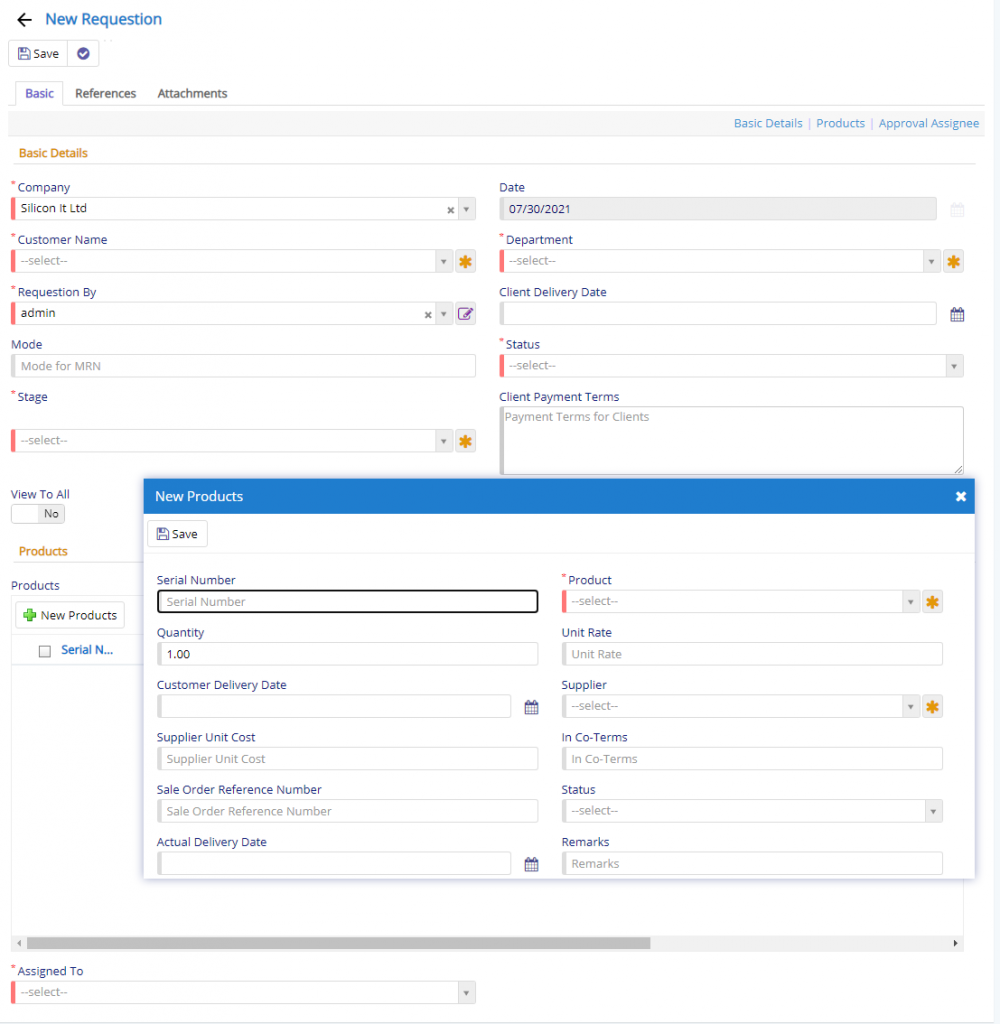
In this page project, company, Material Requisition number, Date, Customer name, Reference, Currency details, Discount details, Printing options, Product details are entered.
Company field will be visible only when you have enabled Multi-company in Company Details and on top of that, if it is enabled in Proforma module.
Material Requisition Number is a custom number field. This field will be visible when the Custom number is enabled in Proforma Settings module. This is useful if you don’t want to use system generated sequence number instead if you want to continue with your own previous sequence number. This field will reset to 1 when the Financial year changes.
Approval fields will be visible only when One or Two Approval mechanisms are enabled.
Reset of the fields are quite self-explanatory.
The fields which are visible here may not be visible to you since these are settings dependent fields. They may be kept disabled or hidden as it not important to your business flow.
Now when you click the New Product button, it invoke a new window as shown above. They have very less fields compared to other modules.
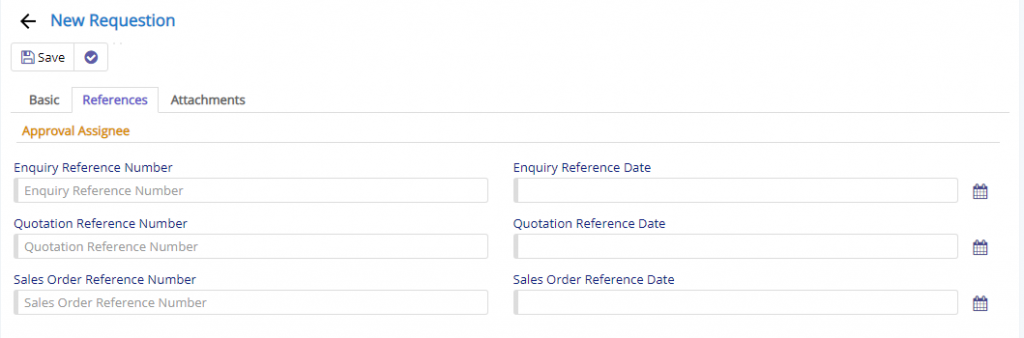
In this block, you have all the reference fields for module like Enquiry, Quotation and Sales Order. These fields will be automatically populated when you move an entry to Material Requisition. Say, if you move an entry from Enquiry to Material Requisition , then Enquiry Number and Date will auto populated. Enquiry Number or any other numbers related to modules are setting dependent. If the Custom number setting is enabled in respective settings of module then, based on the setting the number will be populated.

We have provided eight attachment slots which will allow the user to upload required data in form of files.

- Starting from the left is the Update button which is used to update the changes that you have performed in any of the Tab. This button will change to Save when you are creating a new Entry.
- The Next button which is similar to Update button but the only difference is that, it performs the Update operation and remains on the same page. But the later Updates or Save and returns to the Grid displaying List of users. This button will change its meaning when you are creating a new entry. It will be called as Apply changes.
- The Next button is for Delete, this will delete the selected record from the database.
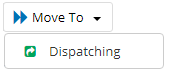
- Dispatching– Material Requisition will be moved to Dispatching module for further processing and dispatching of the products.
Generalized flow of Material Requisition Module
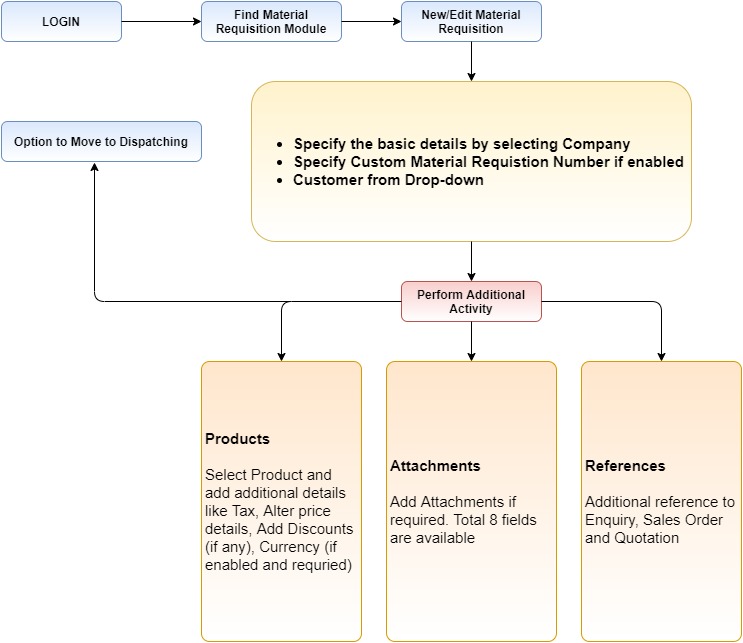